Diamond-like carbon (DLC) coatings have extremely low friction coefficient properties that assist by adding lubricity, which in turn, reduces the pickup of adhesive steel and aluminum particles, and promotes the release of injectable plastic material.
DLC Coatings
DLC COATINGS
The magnetron sputtering systems of eifeler-Vacotec are designed for depositing adhesion-secure and slide-favorable coatings on the basis of MoS2 or DLC.
These coatings are mostly applied for moving parts or tools in order to improve the slide characteristics on the surface. Friction coefficients < 0.1 in contact with steel are easily achieved.
The PVD sputter technology is employed with the DLC layer SUCASLIDE®, CARBON-X® and the solid lubricant layer MoST. The coating is applied here at approx. 200° centigrade.
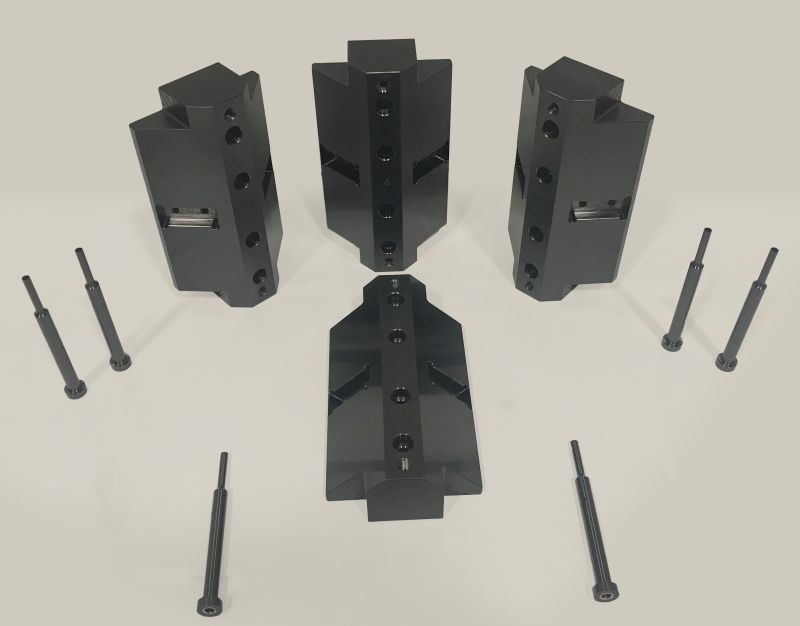
The following advantages result for you:
- Possible combinations with friction reducing layers
- Variable coating structure (nanostructures, multi-layer, monolayer)
- Decoating by chemical and mechanical means
- Very good adhesion on the substrate
- Very good reproduction of textured and polished surfaces
- Very good maintenance of dimensional accuracy and contour-true coating
- No hardness reduction
- No influencing of the crystalline structure of the steel with suitable material selection
Our well-proven and excellent DLC coatings:
- CARBON-X® – Low friction even under tough conditions
- SUCASLIDE® – The modern friction reducing DLC coating
For details on our full North American eifeler coatings network please visit:
https://www.eifeler.com/northamerica/en/
voestalpine eifeler Coatings
EDRO Engineering, INC.
20492 Carrey Road
Walnut,California 91789
Tel: 909-594-5751
coatings@edro.com
Downloads
CARBON-X® (DLC) – Low friction even under tough conditions
CARBON-X® is a new low-friction a-C:H based DLC coating from eifeler.
- Outstanding wear resistance due to high hardness.
- Low friction and reduced sticking of workpiece material
- Enhanced tool performance and longer lifetime
Thanks to its high hardness CARBON-X® is the right choice for applications where high abrasive wear occurs and softer tribological coatings reach their limits.
Additionally, the welding of workpiece material to tooling is significantly reduced resulting in extended tool life.
The design of eifelers CARBON-X® coating delivers top performance even under the toughest conditions.

Applications
- Cutting of non-ferrous metals.
- Blanking/piercing of non-ferrous metals.
- Coldwork.
- Injection moulding tools.
- Components
In Numbers
Hardness: 2,400 ± 400 HV
Max. application temperature: 325 °C / 617 °F
Coefficient of friction: 0.05 – 0.15
Coating thicknesses: 1.5 – 2.5 µm
Color: dark grey
Downloads
SUCASLIDE® (DLC) – The modern friction-reducing DLC coating
Amorphous carbon coating – for use on tools, bearings, and precision components. SUper CArbon SLIDE is a metalliferous, amorphous carbon coating (a-C:Me) from EDRO eifeler. This PVD coating displays all the benefits of a modern, friction-reducing coating:
- Good adhesive strength.
- Very hard.
- Sufficient coating thickness (approx. 2 µm).
- Low friction coefficient.
- Very dense and smooth coating structure.
- Biocompatible.
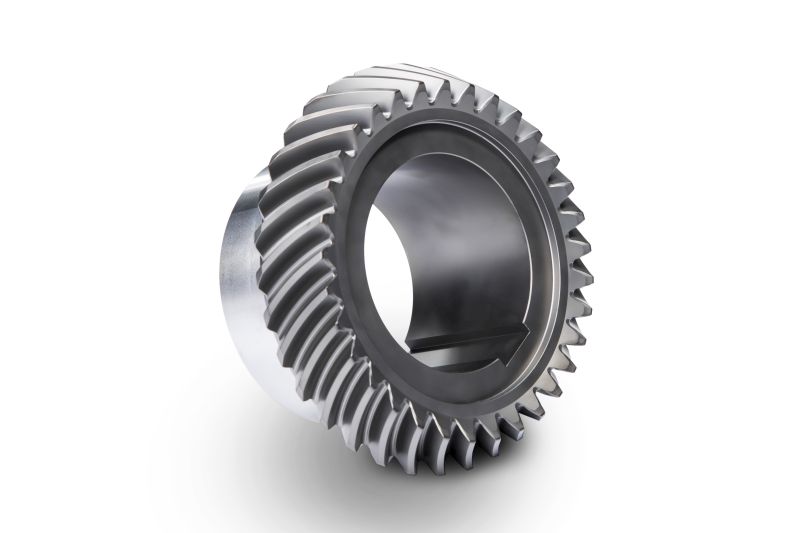
Applications
- Tools: Forming and cutting tools for non-ferrous metals, in particular aluminium (e.g. IHU) Injection moulding tools — for both mould surfaces as well as pushers/ejectors (allows completely dry running)
- Components: Precision components, motor and gearbox parts, gear wheels, bearing and valve parts, sealing and guide elements Paper slitters, industrial blades Food and refrigeration industry components (dry operation) Medical technology
Advantages
- Further significant improvement of the slide characteristics with respect to traditional PVD layers (also with minimal lubrication a significant improvement results) decrease of adhesion and both friction partners are protected.
- Improvement of the run-in characteristics with tools and precision components.
- Improvement of the emergency running characteristics
- Suited for low-tempered steels (case hardened, spring and bearing steels)
In Numbers
Hardness: 1,000-1200 HV
Max. application temperature: 400 °C / 750 °F
Coefficient of friction against steel: 0.05 – 0.10
Coating thicknesses: 1.5 – 2.5 µm
Color: black