The eifeler Duplex Treatment is the combination of a plasma nitriding process with the deposition of an eifeler PVD coating in one uninterrupted process.
Duplex Treatment
Duplex treatment = Plasma nitriding + PVD coating in one process
The combination of a thermochemical plasma nitriding process with the following deposition of a voestalpine eifeler PVD coating in a uninterrupted vacuum system process we call duplex treatment.
The surface hardness of the tool material is definitively increased, which contributes considerably to the increase in performance of the PVD coating. Therefore we developed a nitriding process, suitable for this procedure, where it is performed before the coating process. Basically all coating and nitriding capable steel materials are suited for this process.
Tools are an application emphasis for which this procedure currently is selected regularly and successfully for the forming of high strength sheet materials. VARIANTIC or TiCN is often utilized in this manner.
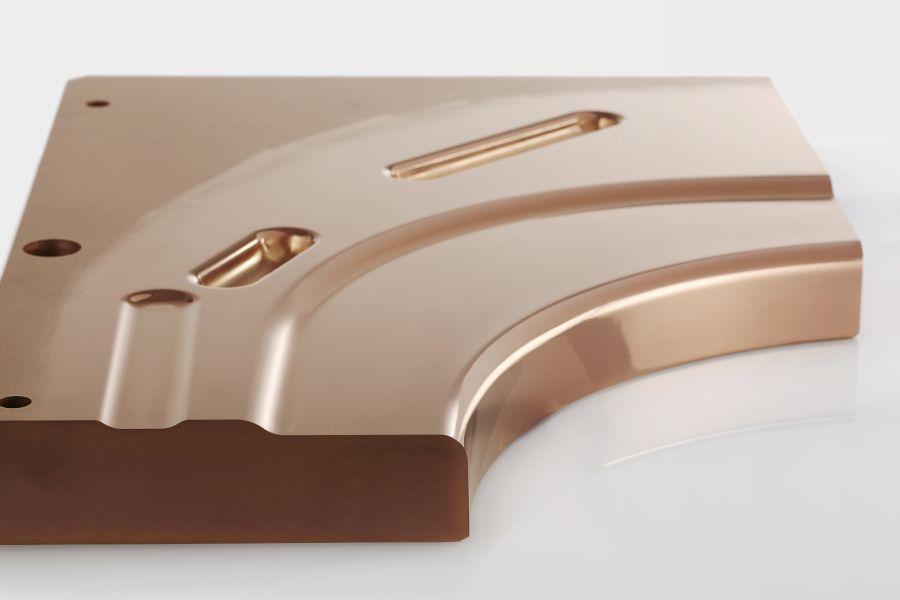
Advantages
- Ideal structure of a hardness gradient from the tough-hard tool core, through a higher supporting hardness in the interface, extending to the extremely hard and wear resistant tool surface.
- A considerably increased support effect therefore results for the extremely hard and brittle ceramic wear protection layer.
- The absorbing ability for pressure loads increases significantly!
Our well-proven and excellent Duplex treatment coatings:
- DUPLEX CROSAL® (ALCRN) – is eifeler’s next generation AlCrN based hard coating.
- DUPLEX CrN / CrCN – For a high level of adhesion
- DUPLEX DUMATIC – Highest levels of hardness and abrasion resistance for forming applications
- DUPLEX TIGRAL – Abrasion resistance and high thermal resistivity
- DUPLEX VARIANTIC – The layer with high oxidation resistance
For details on our full North American eifeler coatings network please visit:
https://www.eifeler.com/northamerica/en/
voestalpine eifeler Coatings
EDRO Engineering, INC.
20492 Carrey Road
Walnut,California 91789
Tel: 909-594-5751
coatings@edro.com
Downloads
Duplex CROSAL® (AlCrN) – That your tools withstand even highest temperatures
CROSAL®-plus is eifeler’s next generation AlCrN based hard coating.
The new coating system is an advanced development of our well-established CROSAL® coating. As a result of optimized process parameters and a tailor-made coating microstructure this versatile high-performance coating covers all key requirements:
- High oxidation resistance
- Outstanding hot hardness
- Excellent coating adhesion
Your plus in metal cutting
CROSAL®-plus is perfectly suited for challenging applications within the fields of dry cutting, punching and forming.
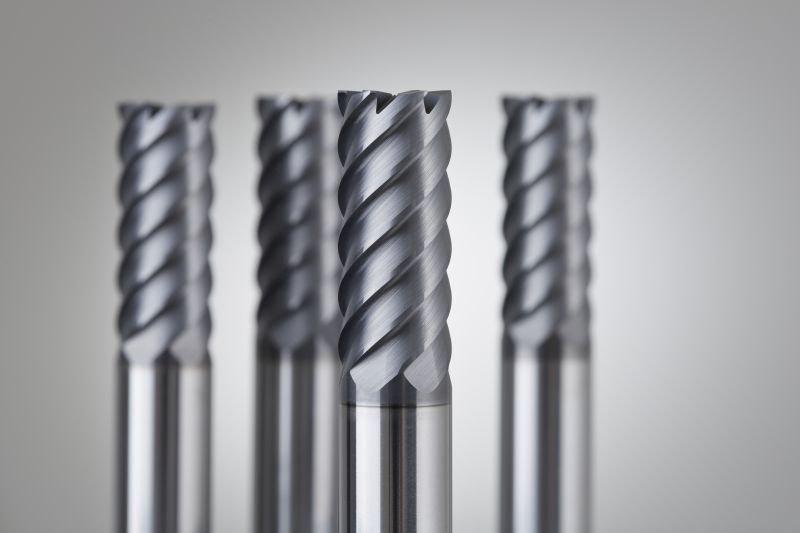
Applications
CROSAL®-plus is especially suited for the following applications:
Cutting
|
Stamping/Forming
|
In Numbers
Hardness: 3.200 ± 300 HV
Max. temperature of operation: 1100 °C / 2012 °F
Coefficient of friction against steel: 0.45
Coating thickness: 2-5 μm
Color: slate-grey
Downloads
Duplex CrN / CrCN – chrome nitride / chrome carbon-nitride – For a high level of adhesion
CrN exhibits good sliding properties with minimal lubrication. The high hardness and very low brittleness allow thicker CrN coatings with very good adhesion to the substrate.
The chrome-nitride coating is characterized by the following properties:
- High hardness and adhesion.
- Very good chemical resistance.
- High-temperature resistance in air
- Thicker layers possible
- Low coefficient of friction against steel
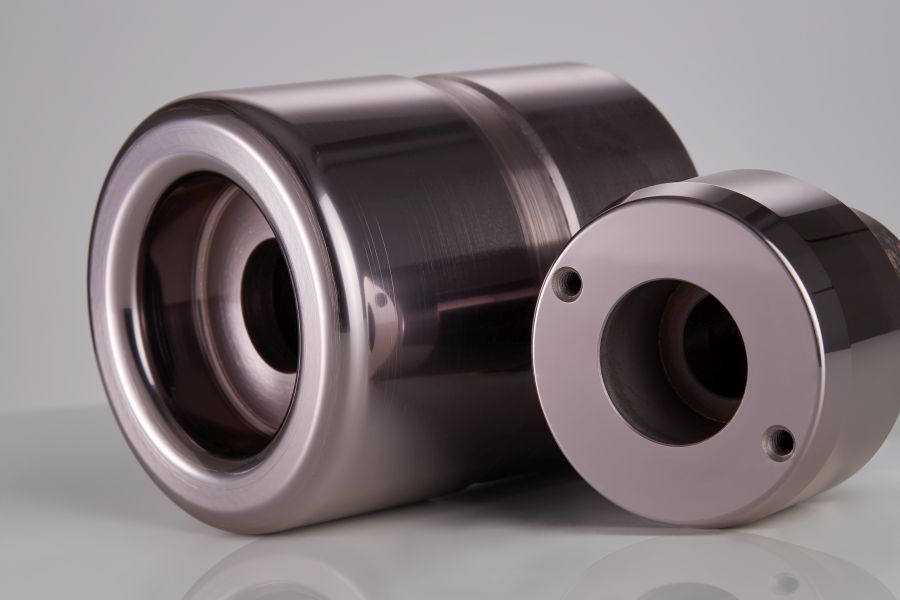
Applications
|
|
In Numbers
Hardness: (CrN) 2,000 ± 200 (CrCN) HV 2,300 ± 200 HV
Max. application temperature: 600 °C / 1,110 °F
Coefficient of friction against steel: (CrN) 0.3 – 0.4 (CrCN) 0.2 – 0.3
Coating thicknesses: (CrN) 1 – 6 µm (CrCN) 2 – 6 µm
Color: (CrN) slate grey (CrCN) silver grey
Downloads
Duplex DUMATIC (TiCN) – Highest levels of hardness and abrasion resistance for forming applications
The new DUMATIC coating is always produced as a duplex version, i.e. using a plasma diffusion process on the base material. The coating has a structured multilayer design with a high proportion of TiC (approx. 4,000 HV). The uppermost layer is designed as a low-friction and colored cover layer
Product Features:
- The DUMATIC coating produced using the PVD process at approximately 450 °C is deposited without any tool distortion
- Polished surfaces are thereby not roughened
- The DUMATIC coating displays a very low tendency for cold welding with high alloy stainless steel qualities
- Due to its relatively low oxidation resistance, DUMATIC is not suitable for higher contact temperatures which can occur with semi-hot forming processes, for example
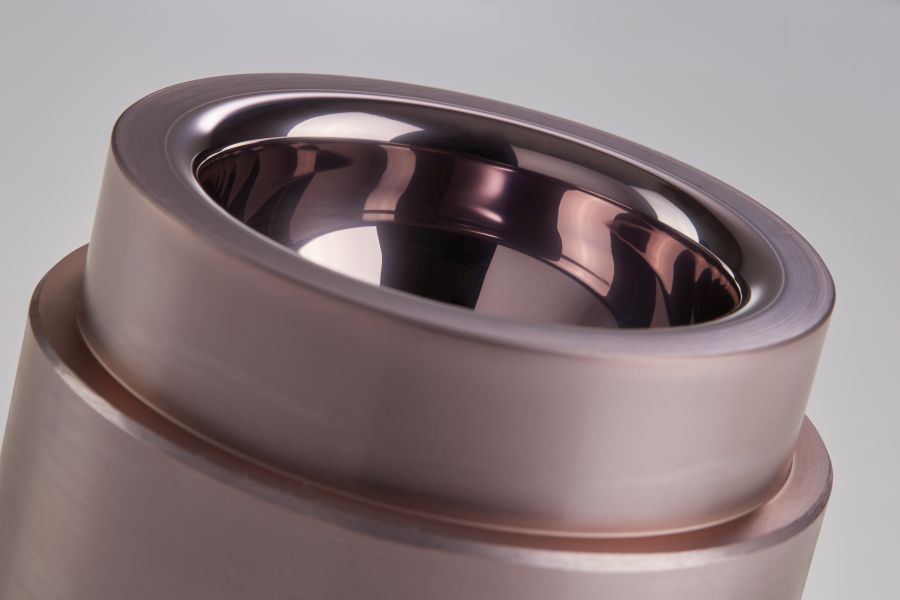
Applications
- Forming technology: Drawing, stamping, pressing and forming tools for the working of high-alloy chrome/nickel materials and similar requirements. Because of its high hardness, it is especially suitable for cold forming and the cutting of high-strength sheet metals and for cold forging processes with high contact pressures.
In Numbers
Hardness: 3,700 ± 500 HV
Max. application temperature: 400 °C / 750 °F
Coefficient of friction against steel: 0.25
Coating thicknesses: 3 – 5 µm
Color: reddish/grey
Downloads
Duplex TIGRAL (TiAlCrN) – Abrasion resistance and high thermal resistivity
This coating, based on AlCrTiN, is characterized by its high hot hardness and its resistance towards oxidation and abrasion. These properties are the result of its nanostructure, which minimizes crack propagation within the coating, especially when subjected to shear loads.
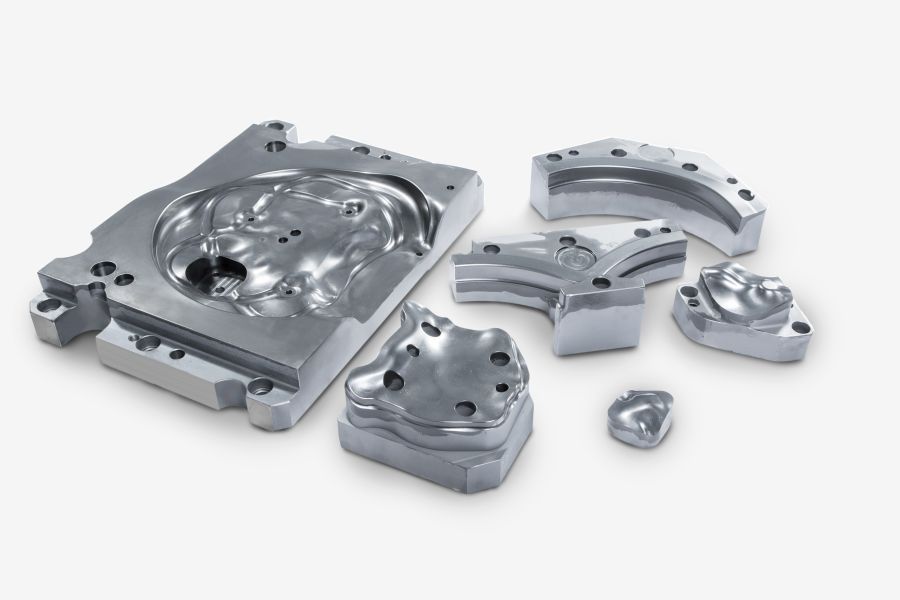
Applications
|
|
In Numbers
Hardness: 3,300 ± 300 HV
Max. application temperature: 900 °C / 1,652 °F
Coefficient of friction against steel: 0.6
Coating thicknesses: 3 – 5 µm
Color: dark grey
Downloads
Duplex VARIANTIC Nitrate (TiAlCN) – The layer with high oxidation resistance
Excellent cutting, forming, stamping and precision cutting results. The temperature resistant TiAlN underlayer, in conjunction with the hard and low-friction TiCN top layer, delivers a combination which presents clear advantages in numerous applications. In the area of cold forming in particular, excellent results are achieved when Duplex VARIANTIC is used.
Property features:
- Can be deposited on HSS and hard metal
- Substantial friction reduction
- Multilayer structure
- High wear resistance
- Tough, hard, and temperature resistant
up to 800 °C
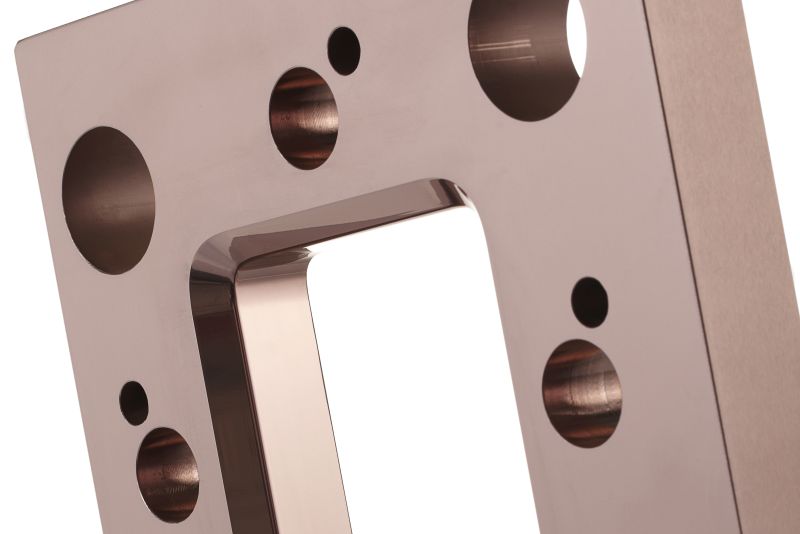
Applications
- Cutting: Milling, turning, drilling and cutting for the processing of high-alloy and low-alloy steels with high feeds and cutting speeds; very well suited for HSS endmills in the area of steel machining.
- Forming: Drawing, stamping, pressing and forming took for the machining of high-alloy and low-alloy steels and e.g. stainless steel sheets.
Deposition technology
The deposition of the VARIANTIC layers is performed by means of PVD technology. This allows the deposition of the coatings on tool steels, HSS, cemented carbides or many other materials with temperatures less than 450° C.
In Numbers
Hardness: 3,500 ± 500 HV
Max. application temperature: 800 °C / 1,470 °F
Coefficient of friction against steel: 0.2
Coating thicknesses: 2 – 4 µm
Color: antique pink