For over 30 years, voestalpine eifeler has created the most innovative PVD coatings on the global market today. Eifeler PVD coatings are ceramic thin films that help protect your substrate by adding hardness, lubricity, and a shield against high working temperatures.
PVD Coatings
PVD COATINGS
Physical vapour deposition (PVD) is used to describe any of a variety of methods to deposit thin films by the condensation of a vaporized form of material onto various surfaces. The metallic elements of the layers consisting of titanium, chrome and aluminum, make a connection to nitrogen and carbon under the impact of a plasma and temperatures of 200 °C to 500 °C. They provide a strong ceramic in this way. The hardness of generated layers are in a range of 1000 to 3800 HV, the coating thickness is between 1 to 10 µm, depending on use.
The PVD hard material coating is carried out at eifeler almost exclusively by means of arc vapor deposition (electric arc vapor deposition ) with temperatures < 450 degrees centigrade. With the arc process technology an excellent adhesion is achieved without hardness loss, distortion or change of the micro-structure of the base material.
Search the voestalpine eifeler coating selection guide to find the coating solution that fits your application.
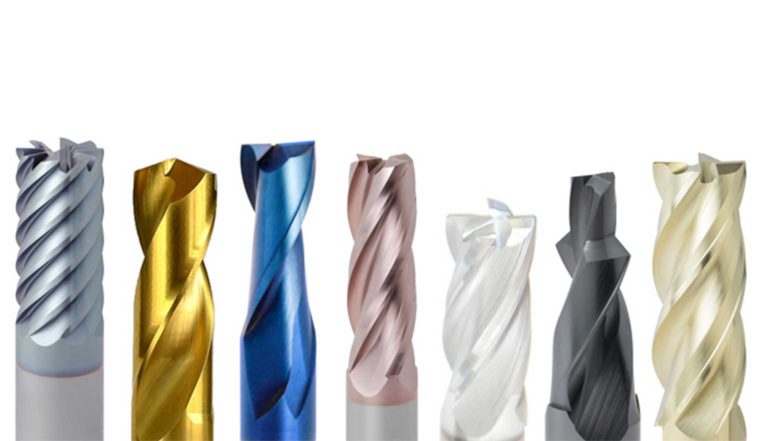
The following advantages result for you:
- Possible combinations with friction reducing layers
- Variable coating structure (nanostructures, multi-layer, monolayer)
- Decoating by chemical and mechanical means
- Very good adhesion on the substrate
- Very good reproduction of textured and polished surfaces
- Very good maintenance of dimensional accuracy and contour-true coating
- No hardness reduction
- No influencing of the crystalline structure of the steel with suitable material selection
Our well-proven and excellent pvd coatings:
- CROSAL®-plus – The new generation of AlCrXN coatings
- CrN/CrCN – chrome nitride/chrome carbon nitride for high level of adhesion
- EXXTRAL-plus – for high-performance machining
- SISTRAL® – the new nano-structured high performace layer
- TiCN – titanium carbonitride, if it should be a little harder than TiN
- TIGRAL – AlCrTiN – abrasion resistance and high thermal resistance
- TiN – titanium nitride, the well-proven all-round coating
- “ultrafine”- Smooth and dense PVD arc coatings from eifeler
- VARIANTIC with high oxidation resistance
- ZrN – Excellent corrosion and abrasive wear resistance
For details on our full North American eifeler coatings network please visit:
https://www.eifeler.com/northamerica/en/
voestalpine eifeler Coatings
EDRO Engineering, INC.
20492 Carrey Road
Walnut,California 91789
Tel: 909-594-5751
coatings@edro.com
Downloads
CROSAL®-plus – That your tools withstand even highest temperatures
CROSAL®-plus is eifeler’s next generation AICrN based hard coating.
The new coating system is an advanced development of our well-established CROSAL® coating. As a result of optimized process parameters and a tailor-made coating microstructure this versatile high-performance coating covers all key requirements:
- High oxidation resistance.
- Outstanding hot hardness.
- Excellent coating adhesion.
Your plus in metal cutting
CROSAL®-plus is perfectly suited for challenging applications within the fields of dry cutting, punching and forming.
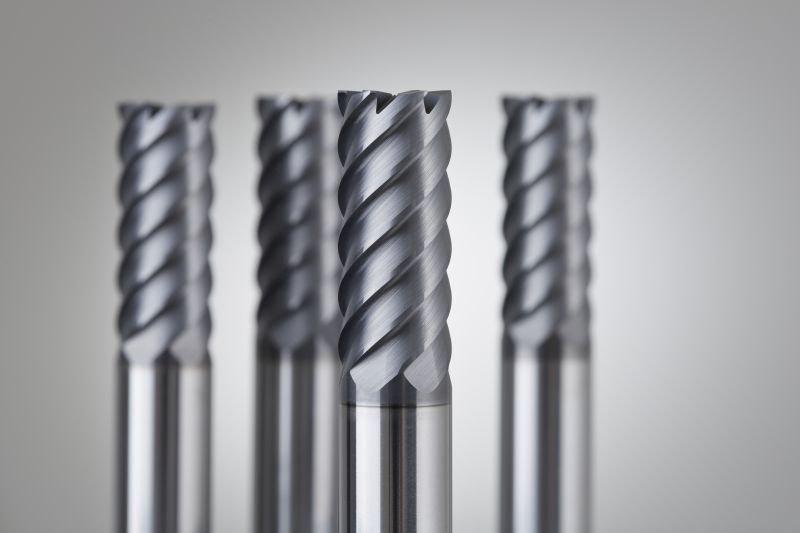
Applications
CROSAL®-plus is especially suited for the following applications:
Cutting
|
Stamping/Forming
|
In Numbers
Hardness: 3.200 ± 300 HV
Max. temperature of operation: 1100 °C / 2012 °F
Coefficient of friction against steel: 0.45
Coating thickness: 2-5 μm
Color: slate-grey
Downloads
CrN / CrCN — chrome nitride / chrome carbon-nitride For a high level of adhesion
CrN exhibits good sliding properties with minimal lubrication. The high hardness and very low brittleness allow thicker CrN coatings with very good adhesion to the substrate.
The chrome-nitride coating is characterized by the following properties:
- High hardness and adhesion.
- Very good chemical resistance.
- High-temperature resistance in air
- Thicker layers possible
- Low coefficient of friction against steel
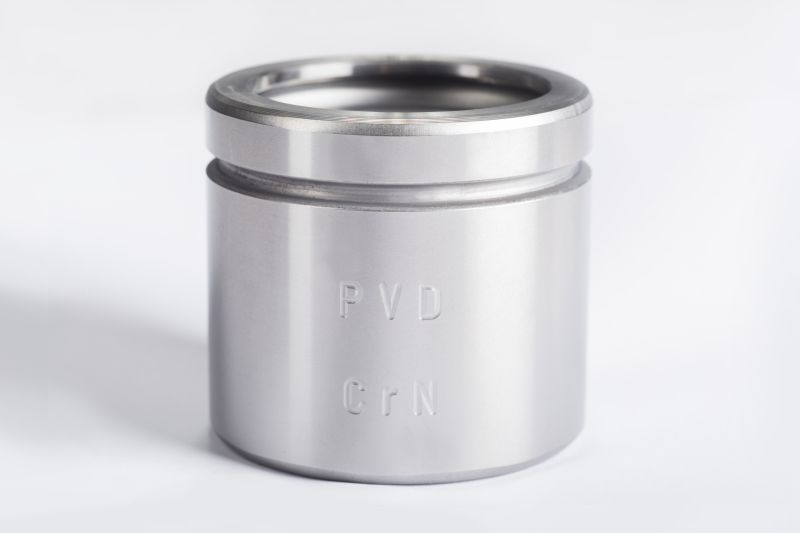
Applications
|
|
In Numbers
Hardness: (CrN) 2,000 ± 200 (CrCN) HV 2,300 ± 200 HV
Max. application temperature: 600 °C / 1,110 °F
Coefficient of friction against steel: (CrN) 0.3 – 0.4 (CrCN) 0.2 – 0.3
Coating thicknesses: (CrN) 1 – 6 µm (CrCN) 2 – 6 µm
Color: (CrN) slate grey (CrCN) silver grey
Downloads
EXXTRAL-Plus – For high-performance cutting
EXXTRAL-plus, a coating based on aluminum-titanium nitride, for the highest requirements in the cutting of hardened steel, M case of high performance cutting with or without cooling lubricant.
The anthracite-colored EXXTRAL-plus is characterized by a very high hardness. The properties are retained up to high thermal and mechanical loads. EXXTRAL-plus is highly inoxidizable and is provided with a low heat conduction coefficient.
- Especially smooth and dense.
- High resistance towards oxidation (800°C)
- High hot hardness
- Enhanced toughness
- Chemical resistance
- Low thermal conductivity coefficient
- Higher cutting speeds
- Longer service life
- Improved surface quality
- Dry machining
- No cooling lubricant required
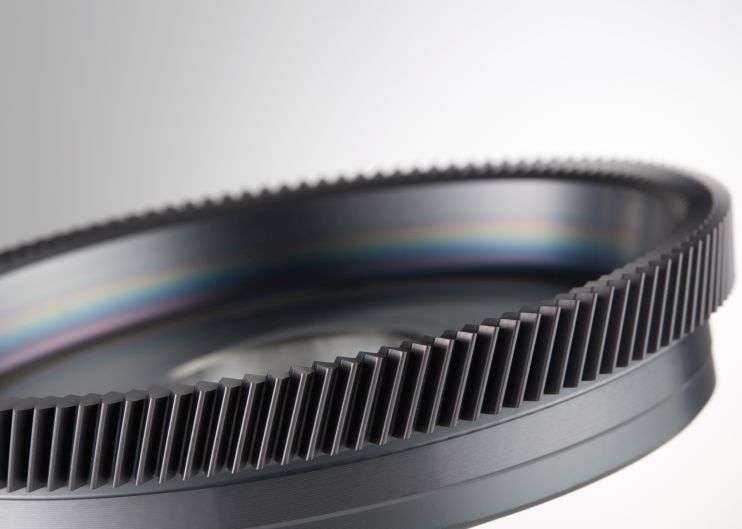
Applications
- Cutting: Because of its multilayer structure, EXXTRAL®-plus is especially recommended for greater coating thicknesses, e.g. for drilling. Resistance towards corrosion is also improved thanks to the greater proportion of chromium.
- Punching: However, EXXTRAL®-plus has also proven itself in other fields: cold and semi-hot forming of steel materials, cutting of thicker sheet steel and the working of aluminum sheet material.
Deposition Technology
- Application of the EXXTRAL layers is implemented by means of POD technology. This allows the deposition of the layer on tool steels, H55, cemented carbides or many other materials with temperatures less than 450° C
In Numbers
Hardness: 3,300 ± 300 HV
Max. application temperature: 800 °C / 1,470 °F
Coefficient of friction against steel: 0.7
Coating thicknesses: 2 – 5 µm
Color: anthracite
Downloads
SISTRAL® – Our new nano-structured high performance layer
SISTRAL® – on the basis of our very successful more advanced EXXTRAL,
- For even higher requirements in case of machining, in the foreground
- For the dry high-speed processing of hardened materials (>54 HRC).
SISTRAL®, which is also anthracite-colored, is characterized by a very high hardness that still protects against wear also at high temperatures, and exceptional oxidation stability.
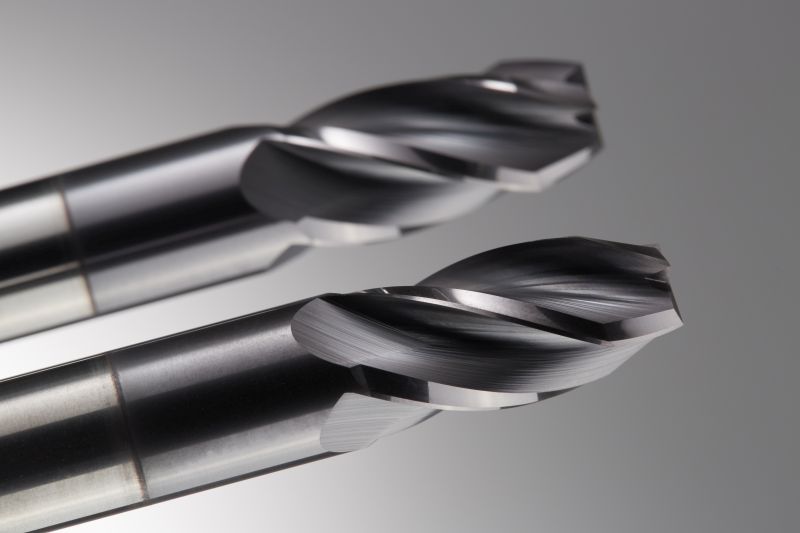
Applications
- Cutting: Developed for metal cutting tasks (milling, drilling, turning, sawing, etc.) under usage conditions where other coatings reach their thermal and mechanical limits. High-performance cutting of very abrasive or hard materials (steel > 54 HRC) in dry, highspeed applications.
- Punching: This nanostructured coating is also well suited to punching, e.g. in stainless steel qualities.
Deposition Technology
- SISTRAL is deposited in the latest eifeler PV0 ARC systems. With temperatures of approx. 450° C high-performance cemented carbides are mainly coated. The coating of tool steels and HS5 is also possible!
In Numbers
Hardness: 3,500 ± 500 HV
Max. application temperature: 900 °C / 1,650 °F
Coefficient of friction against steel: <0.7
Coating thicknesses: 1 – 4 µm
Color: anthracite
Downloads
TiCN – Titancarbonitrid – If it should be a little harder than TiN
Our TiCN is a coating with a complex multilayer structure applied using the arc technique. Despite its great hardness, TiCN is not excessively brittle. This is necessary for numerous applications, such as in interrupted cutting operations when temperatures at the cutting edge are not excessive. Thanks to the reduced friction and enhanced hardness, the use of TiCN coatings often result in a further significant service life extension compared to TiN coated tools.
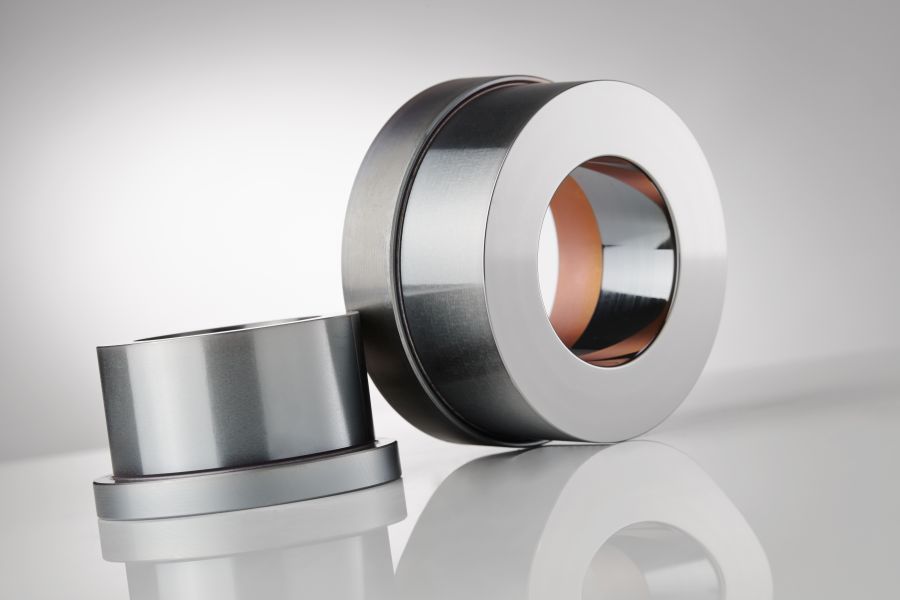
Applications
|
In Numbers
Hardness: 3,500 ± 500 HV
Max. application temperature: 400 °C / 750 °F
Coefficient of friction against steel: 0.2
Coating thicknesses: 1 – 4 µm
Color: blue-grey
Downloads
TIGRAL – Abrasion resistance and high thermal resistivity
This coating, based on AlCrTiN, is characterized by its high hot hardness and its resistance towards oxidation and abrasion. These properties are the result of its nanostructure, which minimizes crack propagation within the coating, especially when subjected to shear loads.
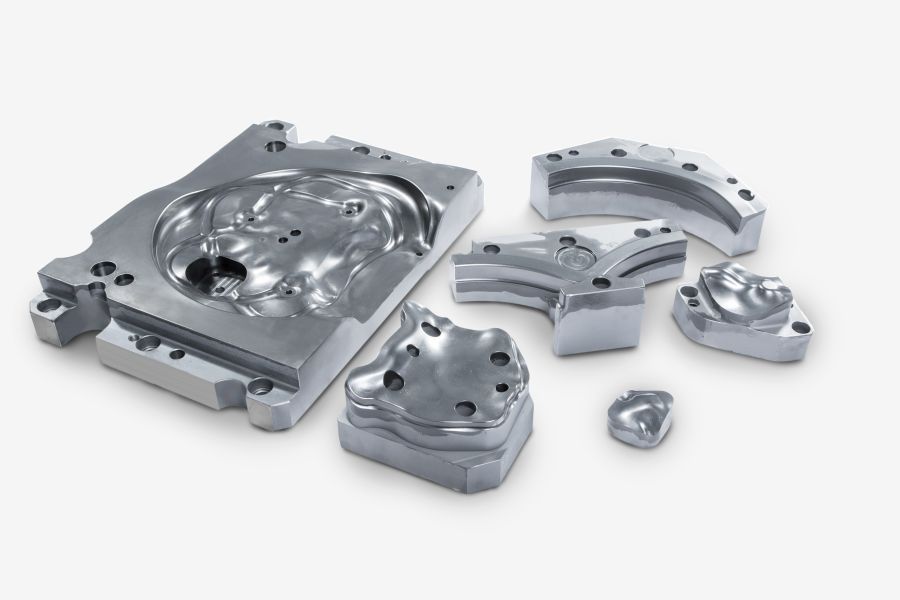
Applications
|
|
In Numbers
Hardness: 3,300 ± 300 HV
Max. application temperature: 900 °C / 1,652 °F
Coefficient of friction against steel: 0.6
Coating thicknesses: 3 – 5 µm
Color: dark grey
Downloads
TIn – Our Well proven all around coating
The titanium nitride layer has for a long time been the well-proven standard layer type through its balanced properties.
- High hardness and adhesion
- Good chemical resistance
- Good temperature resistance in air
- Relatively low thermal conductivity
- Biocompatible and food compatible
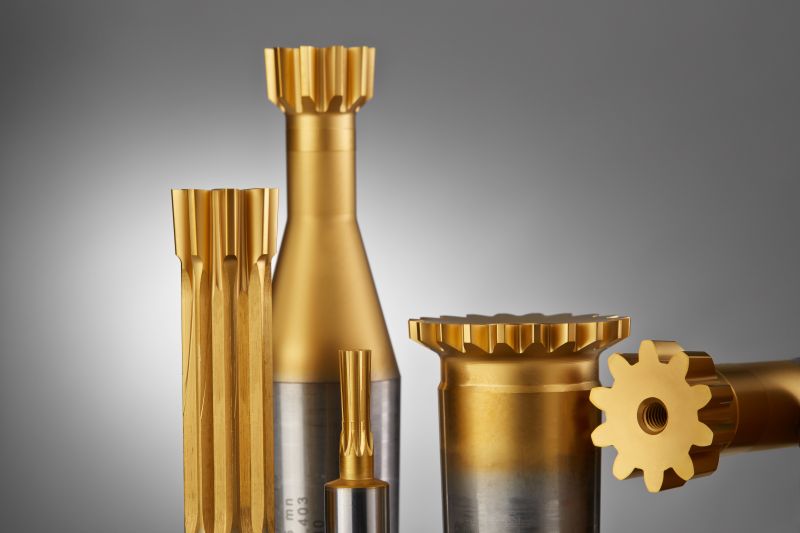
Applications
|
|
In Numbers
Hardness: 2,300 ± 200 HV
Max. application temperature: 500 °C / 930 °F
Coefficient of friction against steel: 0.6
Coating thicknesses: 1 – 4 µm
Color: gold
Downloads
“ultrafine” – Smooth and dense PVD arc coatings from eifeler
“ultrafine” is our label for a line of coatings, which offers the deciding benefit, if smooth and hard PVD arc coatings with very good adhesion are needed.
Smooth is easy! But smooth, well adhesive, hard and economical? This is a challenge. Our SPCS-technology is the solution. SPCS stands for “strongly poisoned cathode surface” and describes our special POD arc deposition technology, leading to outstanding coating properties by an innovative control mechanism of the process gases.
Several serial applications are already established for TN-ultrafine, TICN-ultrafine, and SISTRAL-ultrafine.
These smooth and defect free coatings are characterized by very good adhesion and a high hardness. This gives a benefit for applications like e.g.: cutting, micro-cutting, surgical instruments, and plastic molding.
“ultrafine”: smooth and brilliant PVD arc coatings — even without post finish operations.
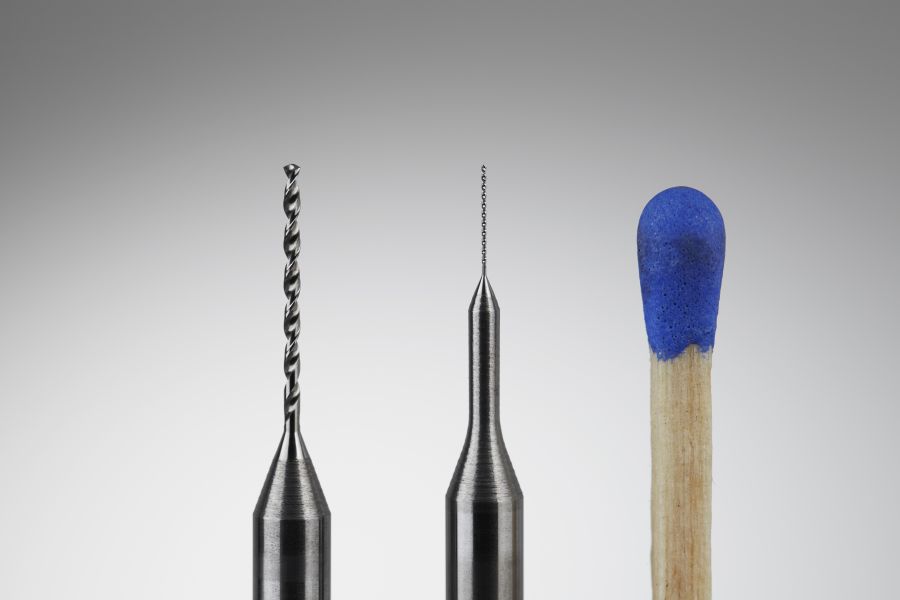
Applications
- Cutting
- Micro-Cutting
- Plastic Molding
- Medical Components
Downloads
VARIANTIC – The layer with high oxidation resistance
Excellent cutting, forming, stamping and precision cutting results. The temperature resistant TiAlN underlayer, in conjunction with the hard and low-friction TiCN top layer, delivers a combination which presents clear advantages in numerous applications. In the area of cold forming in particular, excellent results are achieved when Duplex VARIANTIC is used.
Property features:
- Can be deposited on HSS and hard metal
- Substantial friction reduction
- Multilayer structure
- High wear resistance
- Tough, hard, and temperature resistant
up to 800 °C
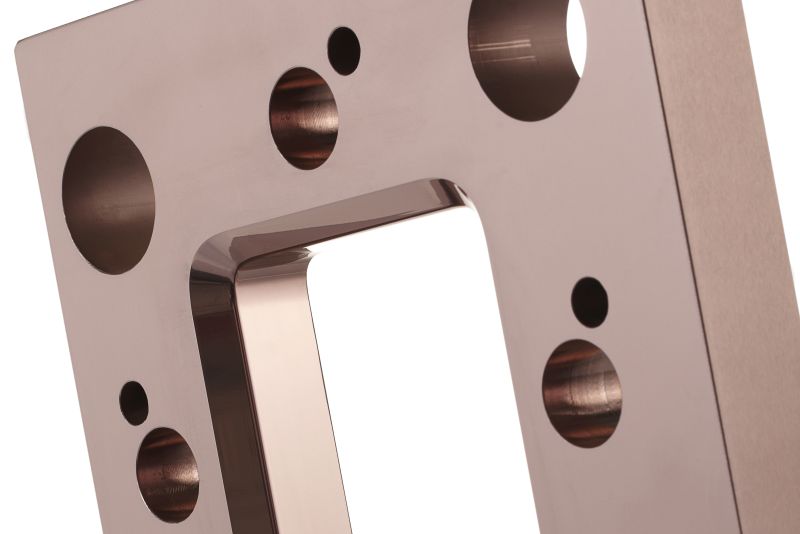
Applications
- Cutting: Milling, turning, drilling and cutting for the processing of high-alloy and low-alloy steels with high feeds and cutting speeds; very well suited for HSS endmills in the area of steel machining.
- Forming: Drawing, stamping, pressing and forming took for the machining of high-alloy and low-alloy steels and e.g. stainless steel sheets.
Deposition Technology
- The deposition of the VARIANTIC layers is performed by means of PVD technology. This allows the deposition of the coatings on tool steels. HSS, cemented carbides or many other materials.
In Numbers
Hardness: 3,500 ± 500 HV
Max. application temperature: 800 °C / 1,470 °F
Coefficient of friction against steel: 0.2
Coating thicknesses: 2 – 4 µm
Color: antique pink
Downloads
ZrN – Excellent corrosion and abrasive wear resistance
The improved ZrN coating is especially suitable for machining aluminum alloys and is also a good choice for machining non-ferrous metals. The ZrN coating is also recommended for machining fiberglass, nylon, and the majority of polymer materials.
The ZrN coating meets all biocompatibility requirements. Thanks to its corrosion resistance and chemical stability, ZrN can be used for medical components coming into direct contact with bones, skin, tissue or blood.
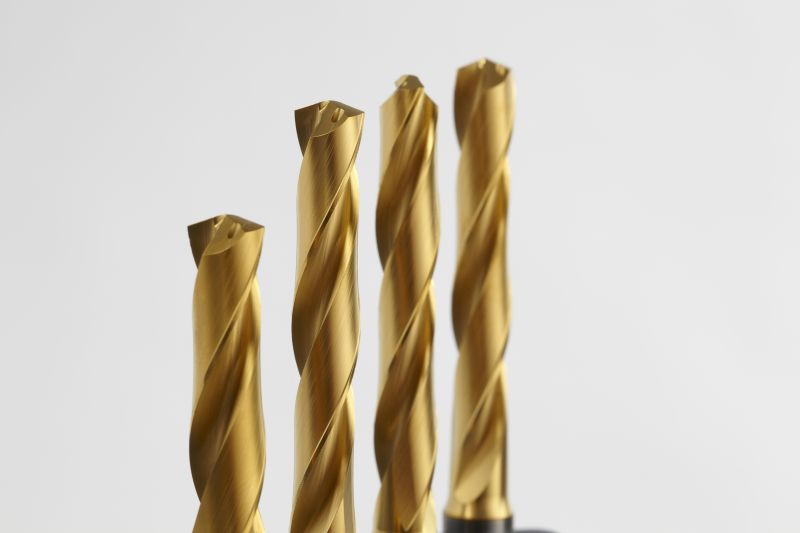
Applications
- Cutting: General high-performance cutting, hobbing, and dry broaching
- Punching and forming : Precision cutting, hot pressing, al die casting, and for applications where the TiN coating could lead to cold welds
- Decorative applications: The ZrN coatings stand out due to its attractive color and effectively protect against abrasive and adhesive wear.
- Medical applications: The ZrN coating meets all biocompatibility requirements. Thanks to its resistance towards corrosion and chemical stability, ZrN can be used for medical components coming into direct contact with bones, skin, tissue or blood.
In Numbers
Hardness: 2,800 ± 300 HV
Max. application temperature: 600 °C / 1,110 °F
Coefficient of friction against steel: 0.5
Coating thicknesses: 1 – 4 µm
Color: light yellow